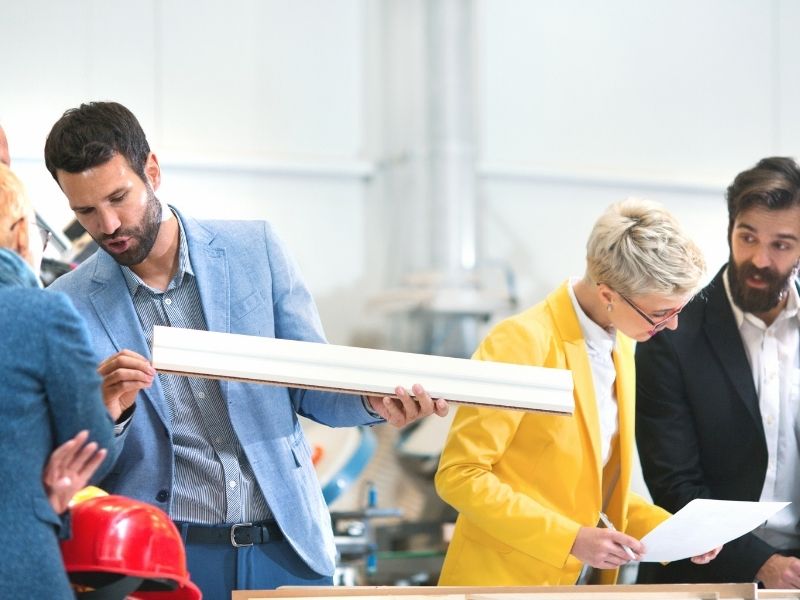
NDT( Non-Destructive Testing Services)
What is Non-destructive testing (NDT)?
Non-destructive testing (NDT) is a form of inspection that takes place without damaging the material or part to be examined.Non-destructive testing methods are used in the detection of discontinuities (corrosion, cracks, structural defects) on the surface of the material or in it.
Non-Destructive Testing (NDT) methods are being used briefly sectors where; production of parts (castings and forgings), automotive, aviation (maintenance, repair and parts in the manufacture of), bridge maintenance, pipe manufacturing, construction, industrial buildings (nuclear reactors) are ranked in the form of Railways.
NDT METHODS
1. Visual Inspection (VT)
The surface of the part with cracks that are invisible to the eye.
The penetrant is applied to the surface.
The excess penetrant is erased.
The crack is made visible by applying the Developer.
It is an examination performed with the naked eye. It is the inspection of parameters affecting the quality such as discontinuities, structural defects, surface condition on the surface of a product using or without using an optical assistant (such as a magnifying glass).
Although visual inspection seems to be a very simple method, it has its own unique subtleties. It is usually a study that must be performed before the application of another nondestructive testing method.
2. Penetrant Inspection
It is an introductory paint inspection. Only defects that have opened on the outer surface of the material can be detected.Only porous materials are not subjected to this examination.
- Pre-cleaning: It is done to clean the impurities oil dirt rust on the surface of the material.
- Penetrating drill: Penetrant liquid is sprayed on the surface, fills the crack. 15 min is expected
- 2. cleaning: it is the cleaning process of the red liquid (penetrant) on the material surface.
- Developer application: It can be applied with water, solvent or spraying. It sucks the liquid out of the crack and pulls it out.
- Examination : It is examined by eye or under fluorine light according to whether fluorescent liquid is used.
3. Inspection with Magnetic Particles
Only examination of ferromagnetic(magnetizable) material can be performed. The part is made into a magnet. If the magnetic field is attracted over the soft iron, it will return to its former state. Even if the magnetic field is removed from C steels, polarization may continue for a while if there are cracks in the material. Transverse errors can be detected with a magnetic field and longitudinal errors can be detected with an electric field.
It can flow easily.The man of the mistake in the faulty material. The resistance he shows to the field is great. If a coil passing an alternating current through it is brought close to a conductive material, vortex purchases are induced in this material. Induced eddy currents create an additional magnetic field. This field can be detected either by the coil that stimulates it personally or by a separate coil. Defects present in the material, geometric and metallurgical changes cause local changes in electrical conductivity and permeability, hence induced eddy currents. These changes in eddy currents are sent by the detector coil to a suitable device. The reading device can be a device with a needle, a scope, a recorder with a pen, a light or sound alarm, a counter, an automatic stamper or a separator device. Thus, the electrical, magnetic and geometric discontinuities of the material can be measured indirectly.
It cannot be applied to non-conductive materials. However, there is an exception to this; the thickness of a non-conductive coating on a conductive material can be measured by eddy currents.
4. Ultrasonic Inspection
In ultrasonic testing, with a central frequency between 0.1-15 MHz and sometimes 50 MHz, very short ultrasonic pulse-waves are initiated to animate the material or the material to detect internal Decays.This technique is also often used to monitor the corrosion of pipework, for example, it determines the thickness of the test object.
However, it can also be used in wood and composite concrete, ultrasonic testing is usually performed on steel and other metals and alloys, though with less solubility.It is a non-destructive form of testing used in many industries such as aerospace, automotive and other transportation industries.
5. Radiographic Examination
Radiographic testing (RT) or industrial X-ray, is a nondestructive testing for hidden defects, short wavelength electromagnetic radiation (high energy photons) by using the general ability to process various materials and inspecting materials (NDT) method.
Either an X-ray machine or a radioactive source (IR-192, Co-60 or, in rare cases, Cs-137) can be used as a source of photons. Neutron radiological testing (NR) is a variant of radiological testing that uses as photons instead of neutrons to process the material.Because neutrons can easily pass through lead and steel but have been stopped by plastic, water and oil, you can see a lot of different things from the X rays.
Since the amount of radiation emanating from the opposite side of the material can be detected and measured, this amount of radiation (or variations in intensity) is used to determine the thickness or composition of the material.